Stainless steel
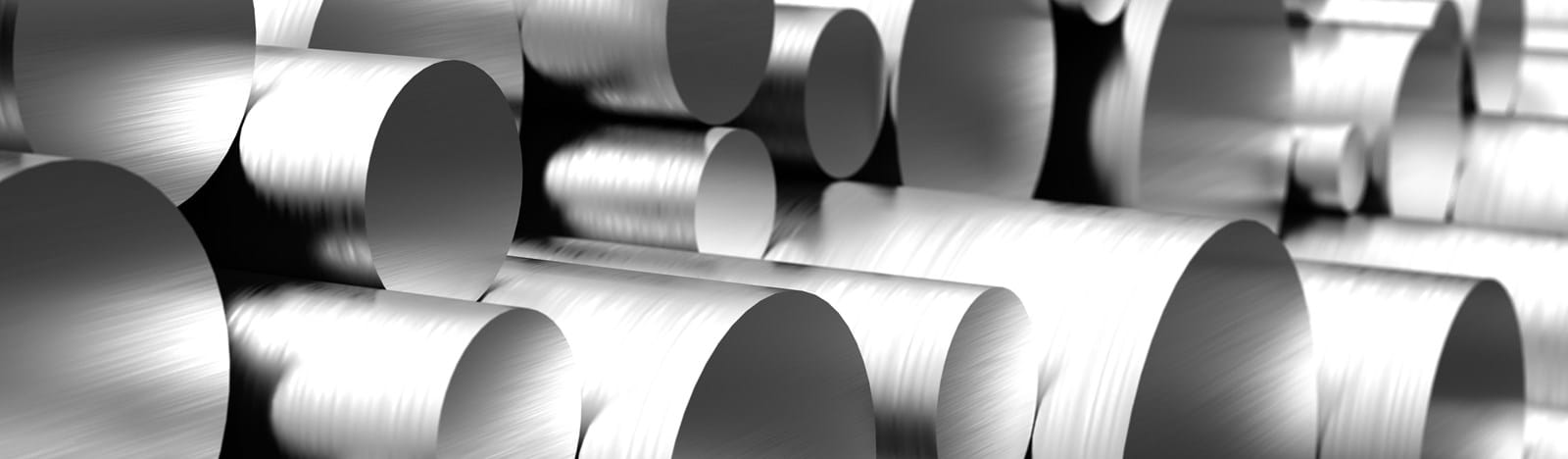
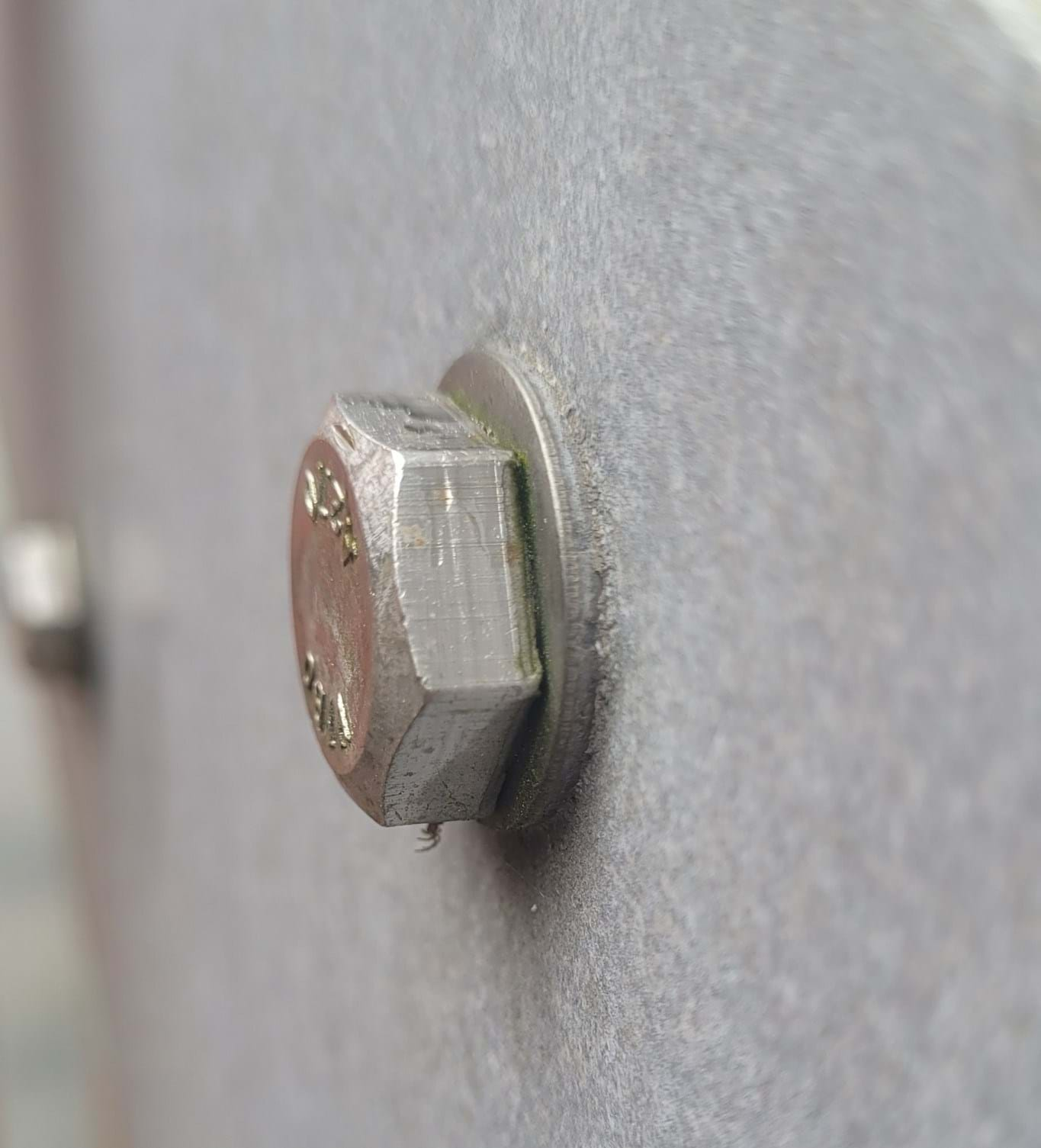
Stainless steel is a term for alloys that meet two criteria:
- The primary metal is iron (Fe)
- Contains a minimum of 10.5% chromium (Cr)
This means that, unlike copper and aluminium, stainless steel is an alloy and not a metal. Steel is not an element in the periodic table.
In addition to chromium, stainless steel alloys often contain metals such as nickel, manganese and molybdenum – alloys with a high molybdenum content are what we know as "acid-resistant" grades.
Stainless steel was invented in the early 1900s, making it a relatively new material. But due to the obvious advantages of the material, it quickly became popular and is one of the most widely used materials in the industry today.
What is stainless steel used for?
Everything from kitchen sinks to machine parts and large tank systems are made from stainless steel because it is durable (under the right conditions) and is generally suitable for machining.
Food and pharma
Tank and pipe systems in the food and pharmaceutical industries are some of the typical applications for stainless steel. The advantages of stainless steel in this context are low surface roughness and good corrosion resistance, both making the surface easier to keep clean.
In the food and pharmaceutical industries, entire process plants are built from stainless steel plates, bars and fittings.
If the steel is to be used in food production, you must have a declaration of conformity to prove that the steel is approved for food contact. You can find all Alumeco declarations of conformity here.
Machining
Stainless steel is generally suitable for machining. Common methods of machining and fabrication are e.g. milling, turning, welding and bending.
Types of stainless steel
Stainless steel is generally divided into three main types:
- Austenitic
- Ferritic
- Martensitic
In addition, these primary types can be combined into the subtypes duplex and super austenitic stainless steel.
The five types of steel each have their own characteristic alloy composition and consequently different strengths and weaknesses.
Physical properties
|
Unit |
Austenitic EN1.4404 (316L) |
Ferritic EN1.4016 (430) |
Martensitic EN1.4057 (431) |
Density |
g/cm3 |
7.9 |
7.7 |
7.0 |
Melting point |
°C |
1375-1400 |
1425-1510 |
1430-1510 |
Young’s modulus |
MPa |
200,000 |
200,000 |
215,000 |
PREN* |
|
23.1 |
16.0 |
15.0 |
Coefficient of thermal expansion |
µm/m*K |
16.0 |
10.5 |
10.0 |
*Higher PREN value = better corrosion resistance
How to calculate thermal expansion
Stainless steel will expand and contract depending on the temperature.
To account for this, you need to calculate the thermal expansion when the steel is to be used in an environment with large temperature fluctuations. To give an example, the outdoor temperature in Northern Europe can easily vary from -20 °C to +30 °C.
The thermal expansion is calculated using the coefficient of thermal expansion (see table under Physical properties).
Example
- A 4404 sheet (coefficient of thermal expansion: 16.0 μm/m*K) is mounted on a façade.
- At -20 °C, the plate is 1000 mm
- At +30 °C, i.e. 50 degrees warmer, the thermal expansion is:
16 μm/(m*K)*1 m*50 K=800 μm=0.8 mm
The sheet is 1000.8 mm at +30 °C.
What is rolling direction?
When a sheet is rolled, the rolling process leaves lines in the material.
The lines are visible on the finished plate, so in some cases it is necessary to account for the rolling direction.
To create a uniform look, panels should be mounted so that the structural lines go in the same direction.
If the plate is to be bent, the rolling direction can affect the bending ability.
To avoid any problems, we ask you to specify the rolling direction when buying sawn sheets/plates. This ensures that the finished sheet has the right properties in relation to the length and width. In this example, the rolling direction of the sheet is 300 mm:
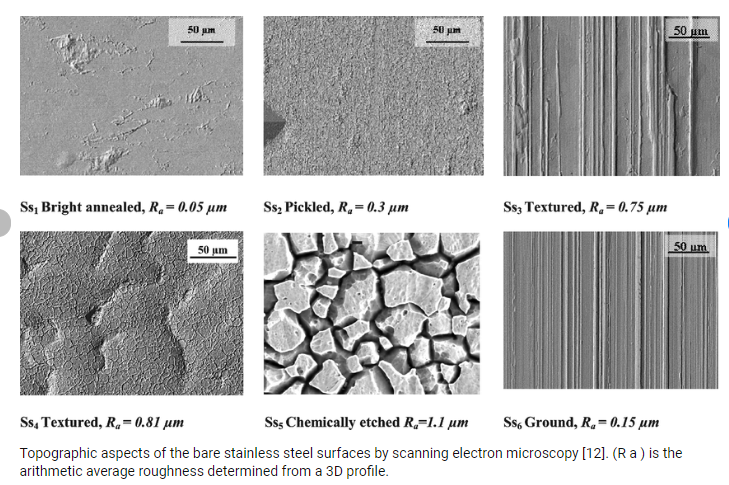
The most common chemical surface treatments are:
- Pickling
- Passivation
- Decontamination
- Electropolishing
The typical types of mechanical surface treatment are:
- Glass blasting
- Grinding
- Polishing
Depending on the type and intensity of the surface treatment, the end result can vary greatly. To ensure a common frame of reference, the surface quality of stainless steel is defined in EN 10088-2.
How to clean stainless steel
Under normal atmospheric conditions and in a clean environment, there is no risk of corrosion of stainless steel – provided the right quality has been chosen for the purpose.
But in the real world, things are not that simple. Stainless steel will often be exposed to foreign substances and dirt for various reasons, for example in a production facility or outdoors.
In these situations, it is important to keep the material clean to reduce the risk of corrosion.
Guidelines for cleaning
The smoother the surface, the easier it is to keep clean. Help yourself by taking maintenance into account when choosing the surface quality.
It is also important to design the surface so that water and dirt can drain away instead of settling in grooves and corners. With an outdoor construction, rain can take care of most of the cleaning if the design allows for it.
If parts of the structure are sheltered from rain, manual cleaning may be necessary. This will remove airborne contamination such as salt from the sea and air pollution.
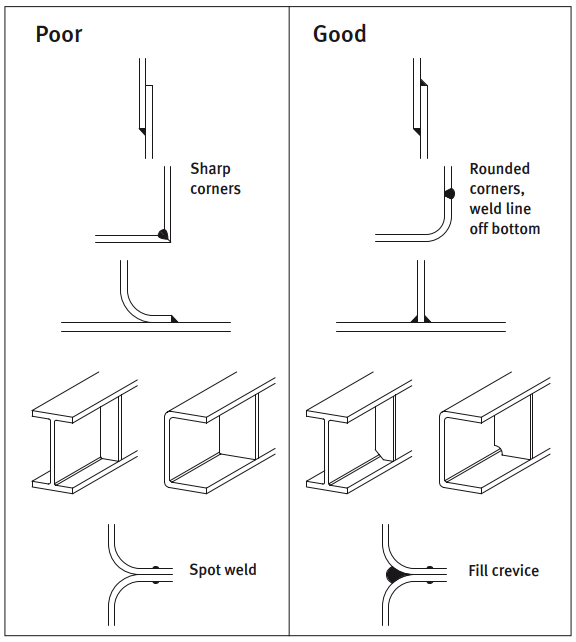
Cleaning agents
The surface of stainless steel is fairly robust and can withstand most cleaning agents. However, you rarely need more than regular soapy water and a soft brush, possibly 5% ammonia for the tougher dirt and grime.
Regardless of the cleaning agent, the surface must be rinsed with water before and after cleaning.
We recommend the following cleaning agents for stainless steel - the list is ranked from the most gentle method (soapy water) to the most aggressive (abrasives):
- Ordinary soap
- 5% ammonia solution
- Solvents, e.g. kerosene, turpentine or white spirit
- Polishing with wax (may temporarily damage the oxide layer)
- Sanding with wax (may temporarily damage the oxide layer)
- Abrasive cleaner (may temporarily damage the oxide layer)
To prevent minor blemishes such as fingerprints, you can use a cleaning agent with a protective effect.
Learn more in the Euro Inox guide on cleaning architectural stainless steel.
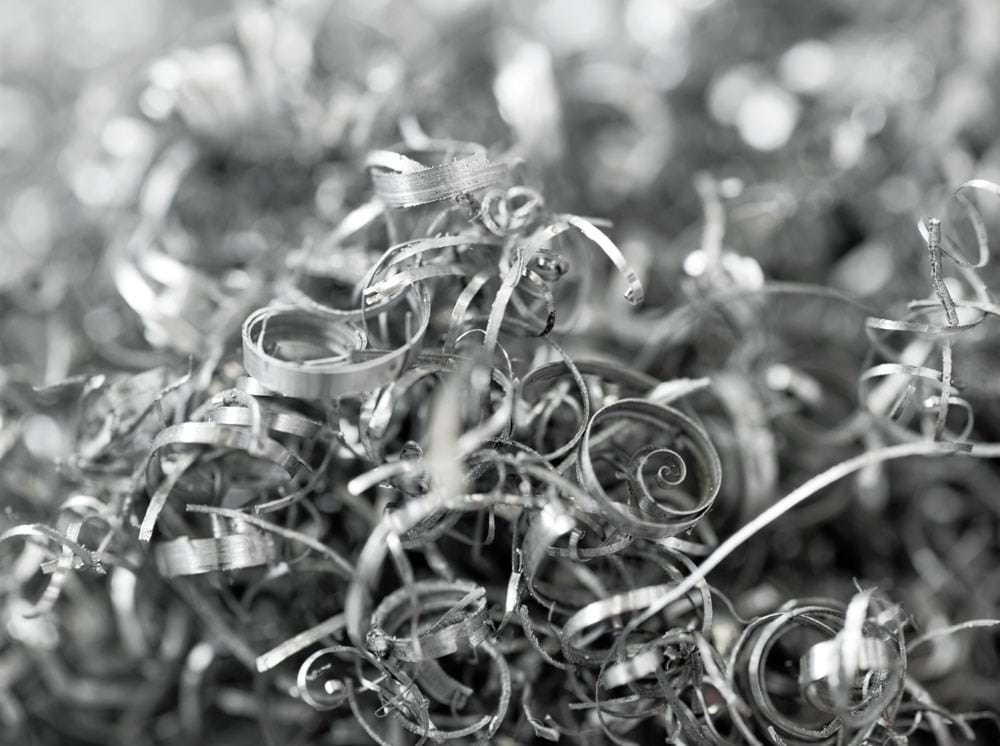
Recycling saves a significant amount of energy compared to mining and producing the raw materials from new.
But in order to recycle efficiently, the stainless steel needs to be of the right quality and in sufficient amounts. If there is not enough scrap of the alloy in question, it is still necessary to mine and add new raw materials to get the right material composition.
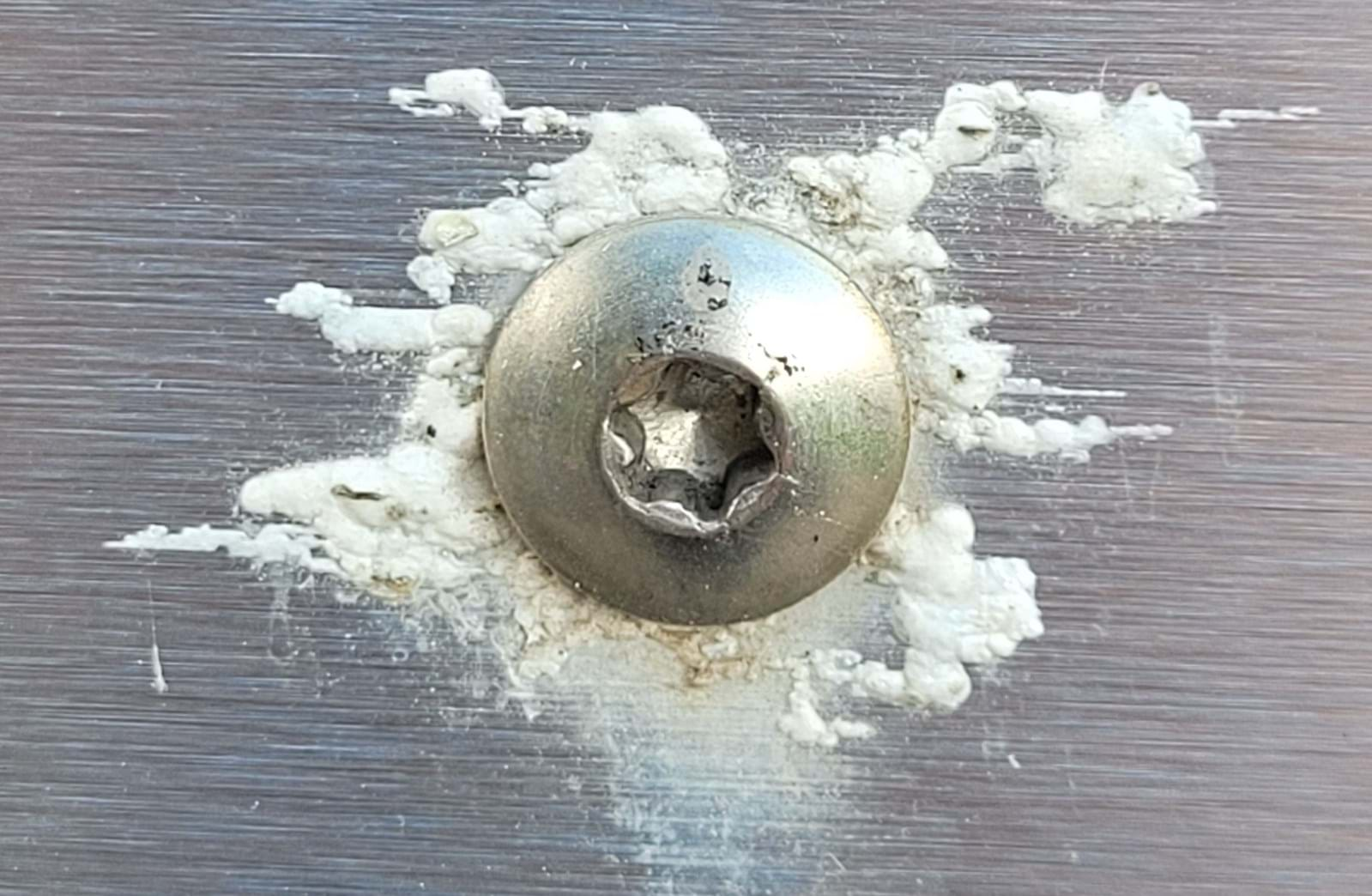
Stainless steel corrosion
The name says it all: Stainless steel is highly resistant to corrosion. However, stainless steel is far from immune to corrosion – it is not “stainless” in all situations.
But if you choose the right alloy for the intended environment – and take the necessary precautions – stainless steel can last for many years.
Oxide layer
The reason is that stainless steel forms a natural, protective oxide layer. The layer forms relatively quickly and restores itself when damaged, keeping the material safe at all times.
As long as the oxide layer is intact, stainless steel can withstand almost anything (with the right alloy in the right environment). However, if the oxide layer is damaged and not given a chance to recover, corrosion can accelerate very quickly.
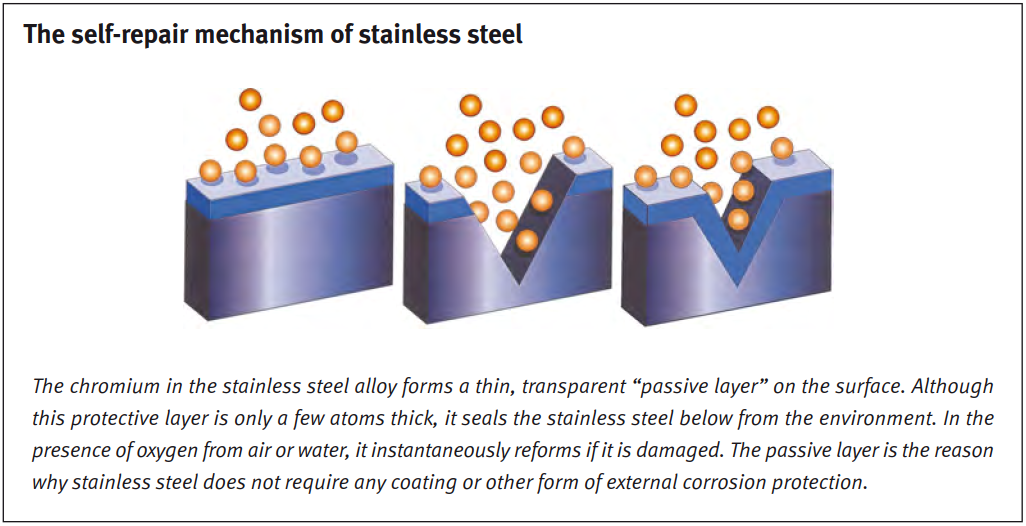
Alloying elements and corrosion
Since stainless steel is by definition an alloy, you can adjust the properties of the steel by adjusting the alloying elements. The four most relevant alloying elements in relation to corrosion are chromium, molybdenum, nickel and carbon.
Chromium
Chromium is the defining alloying element in stainless steel and also what makes the steel itself "stainless". Chromium is the primary ingredient in the oxide layer and essential for the steel’s ability to protect itself.
The chromium content is at least 10.5% (EN 10 020), often much higher.
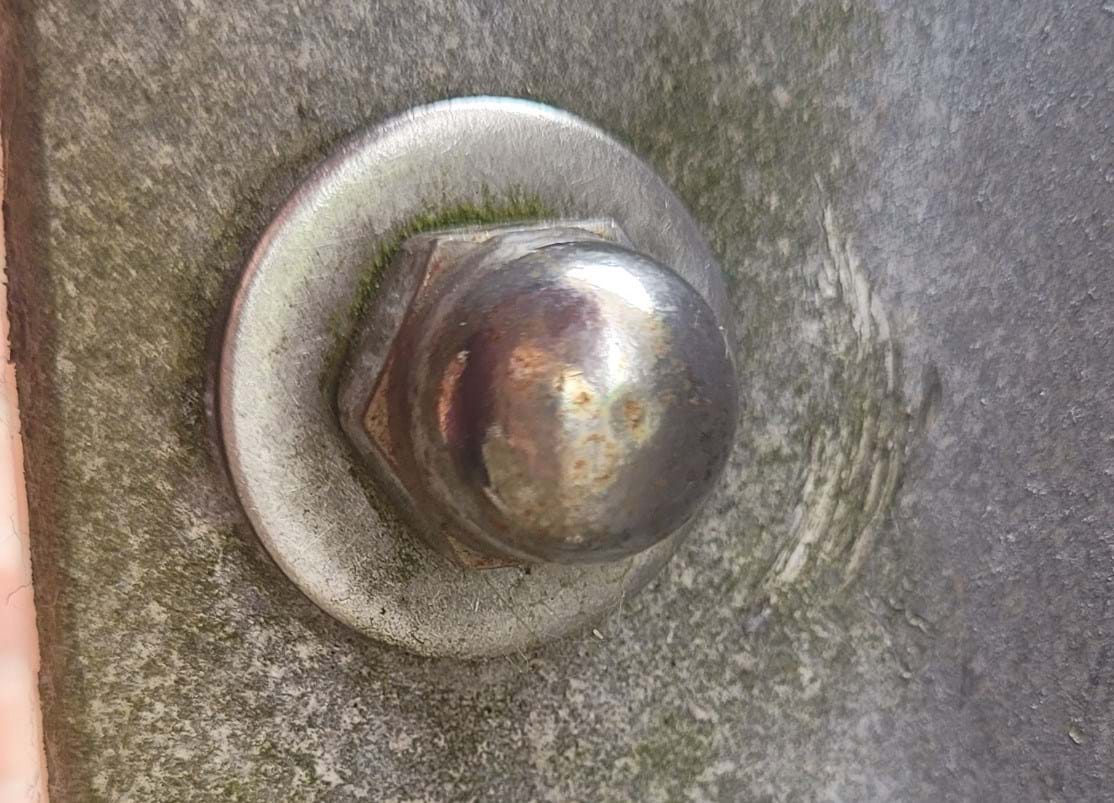
Molybdenum
Molybdenum is another element added to increase the corrosion resistance, and it is particularly known from the "acid-resistant" grades such as 4404 or 4401.
Chemically, molybdenum is very similar to chromium, but it protects more effectively against corrosion – which is why the alloys have been nicknamed "acid-resistant".
The molybdenum content is typically 0-6%.
Nickel
Nickel is the most important alloying element in austenitic stainless steel (8-25%), and, generally speaking, it increases corrosion resistance. In martensitic and ferritic alloys, the content is less than 7%.
Carbon
In stainless steel, carbon is considered a contaminant, which typically comes from recycled iron. We prefer to have as little carbon as possible in stainless steel.
Carbon tends to build up between the metal crystals and cause intergranular corrosion.
Martensitic steel can have a carbon content of up to 1.2%, but otherwise the carbon content of stainless steel is barely noticeable.